Collaborative Robotics: Transforming Manufacturing for Efficiency and Safety
EPA System / News & Eventi
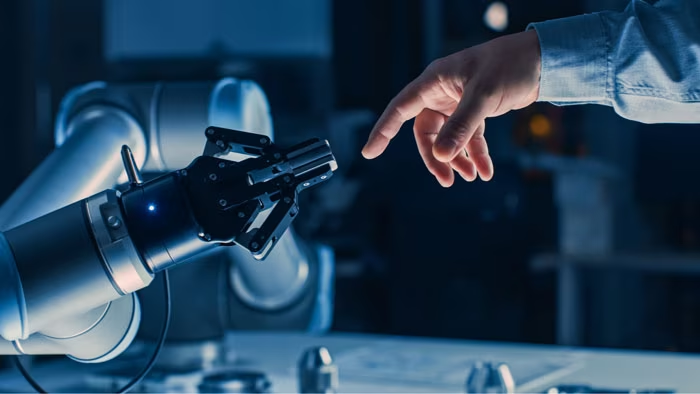
Collaborative robotics, also known as cobotics, has revolutionized the manufacturing industry by ushering in a new era of efficiency and safety on production lines. Unlike traditional industrial robots, cobots are designed to work alongside humans, offering a range of significant advantages. In this section, we will explore what collaborative robotics is and how it has transformed the manufacturing industry.
Collaborative robotics is based on the collaboration between humans and robots, allowing them to work together in the same environment without the need for physical barriers. Cobots are designed to be safe, user-friendly, and highly flexible. This means they can be easily integrated into existing production lines, improving efficiency and reducing risks for human operators.
### How Collaborative Robotics Enhances Production Line Efficiency
One of the main advantages of collaborative robotics is the improvement of production line efficiency. By working alongside human operators, cobots can perform a variety of repetitive and strenuous tasks, freeing up human operators to focus on higher-value tasks. For example, a cobot can be programmed to handle assembly or packaging operations, enabling human operators to concentrate on design or quality control activities.
Moreover, cobots can work continuously without fatigue or errors. This ensures consistent and high-quality production, minimizing waste and machine downtime. Additionally, cobots can be easily reconfigured to meet changing production needs, allowing companies to be more agile and responsive in the market.
### The Impact of Collaborative Robotics on Production Line Safety
In addition to improving efficiency, collaborative robotics has a significant impact on production line safety. Cobots are designed to be safe for use in the presence of human operators, thanks to a range of integrated safety measures. For instance, cobots are equipped with advanced sensors that detect the presence of people nearby, enabling them to slow down or stop completely to avoid collisions or injuries.
Furthermore, cobots are designed to be ergonomic and intuitive to use, reducing the risk of musculoskeletal injuries or fatigue for human operators. With these features, cobots help create a safer working environment where human operators can collaborate with robots without concerns for their safety.
### Case Studies of Companies Using Collaborative Robotics in Production Lines
To better understand the impact of collaborative robotics on production lines, let’s examine some case studies of companies that have successfully implemented this technology. In the automation sector, a manufacturing company introduced cobots into its production line to handle assembly tasks. Thanks to the cobots, the company increased production by 30% and reduced errors by 20%. Human operators were trained to supervise the cobots’ operations and intervene only when necessary.
Another electronics company incorporated cobots into its production line for welding operations. Due to the precision and consistency of cobots, the company achieved a 25% increase in quality and a 15% reduction in waste. Human operators, instead of engaging in repetitive and strenuous welding tasks, were trained for more complex quality control tasks, further enhancing the production process.
### Innovations in Collaborative Robotics Technology
Collaborative robotics technology is evolving rapidly, introducing new innovations that further expand the possibilities of cobot use in production lines. One major innovation is the introduction of cobots with artificial intelligence and machine learning capabilities. These cobots can learn and adapt autonomously to new situations, continually improving their performance and enabling the automation of even more complex tasks.
Another innovation is the integration of cobots with technologies such as computer vision and advanced sensing. These technologies allow cobots to detect and manipulate objects even more precisely, opening the door to new applications in handling delicate or intricate materials. Additionally, integrating cobots with augmented reality devices can further enhance the efficiency and safety of production lines, providing human operators with real-time information on tasks to be performed.
### Challenges in Implementing Collaborative Robotics in Production Lines
Despite numerous advantages, implementing collaborative robotics in production lines may pose some challenges. One of the main challenges is the need to train human operators in using cobots and integrating them into existing production processes. Providing adequate training is essential to ensure that human operators can use cobots safely and efficiently.
Another challenge is the integration of cobots with an organization’s existing IT systems. Ensuring that cobots can communicate and exchange data with other production systems, such as inventory management or production planning systems, requires close collaboration between the IT and production departments of the organization to ensure smooth implementation.
### Best Practices for Integrating Collaborative Robotics in Production Lines
To ensure successful integration of collaborative robotics into production lines, it is important to follow some best practices. Firstly, it is advisable to start with a detailed assessment of production processes and identify tasks that can be automated using cobots. This will help focus implementation efforts on tasks that offer the highest return on investment.
Secondly, involving human operators from the early stages of the implementation process is crucial. Human operators can provide valuable insights into the specific needs and challenges of production lines, helping ensure that cobots are designed and configured optimally for their use.
Finally, continuously monitoring and evaluating the effectiveness of cobots in production lines is essential. This will help identify any areas for improvement and make necessary changes to maximize efficiency and safety.
### Future Trends of Collaborative Robotics for Production Lines
Collaborative robotics is set to play an increasingly important role in the production lines of the future. One emerging trend is the interconnection of cobots through the so-called “Internet of Robotic Things.” This interconnection will allow cobots to exchange information and collaborate autonomously, further enhancing the efficiency and flexibility of production lines.
Another trend is the integration of cobots with data analytics and artificial intelligence. This will enable cobots to analyze production data in real-time, identify anomalies or inefficiencies, and make necessary changes to optimize production line performance.
### Training and Certification for Working with Collaborative Robotics
To successfully work with collaborative robotics, proper training and certification are necessary. Organizations must provide their human operators with specific training on cobots, including safety principles, programming software usage, and best practices for collaborating with robots. Additionally, it is important to ensure that human operators are aware of the rights and responsibilities related to the use of cobots.
Certification programs also exist to attest to the competence of human operators in using cobots. These certifications can be valuable in demonstrating the level of expertise and increasing the confidence of customers and business partners.
### Conclusion: The Future of Collaborative Robotics in Improving Production Line Efficiency and Safety
Collaborative robotics has proven to have a significant impact on the efficiency and safety of production lines. Thanks to their ability to work alongside human operators, cobots enhance efficiency, reduce safety risks, and enable companies to be more agile and competitive in the market.
With the evolution of technology and the introduction of new innovations, such as artificial intelligence and cobot interconnection, the future of collaborative robotics looks even more promising. Companies that embrace this technology and invest in the training and certification of their human operators will gain a significant competitive advantage in the manufacturing industry.